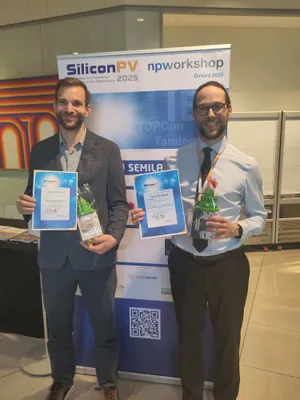
Unsere Forschung
Die Energiewende braucht die Solarenergie. Solarenergie schont unser Klima, ist überall verfügbar, ist bei der Bevölkerung beliebt und erzeugt Strom und Wärme nahe dem Ort des Energiebedarfs. Und: Der weltweit rasante Ausbau der Solarenergie birgt große wirtschaftliche Chancen für unser Exportland!
Seit mehr als 30 Jahren fördern wir die Nutzung der Solarenergie durch unsere angewandte Forschung und die Ausbildung junger Menschen in den Bereichen „Photovoltaik“ und „Solare Systeme“. Dabei ist „Innovation mit Wirkung“ unser Motto. Wir kooperieren intensiv mit der Industrie, mit anderen Forschungseinrichtungen und Universitäten und sind ein An-Institut der Leibniz Universität Hannover.
Wir freuen uns auf Ihre Anfragen, sei es als möglicher Forschungspartner aus der Industrie oder als Kunde unseres Dienstleistungsangebots oder in Form Ihrer Bewerbung für eine der ausgeschriebenen akademischen Abschlussarbeiten und Stellenangebote. Ihre Ideen zählen!
Aktuelle Meldungen
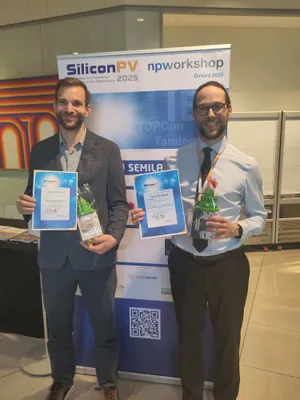
.jpg-400w.webp)
Strategisches Positionspapier zur Stärkung der Solarindustrie – Impulse für die Koalitionsverhandlungen 2025
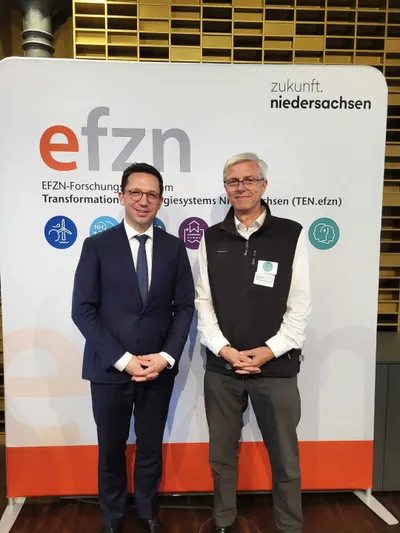
Kick-off des Forschungsprogramms „Transformation des Energiesystems Niedersachsen“ (TEN.efzn)
Natürlich mit Bioenergie
Forschende der Leibniz Universität Hannover und des ISFH haben eine Stellungnahme zu einem Fachartikel veröffentlicht. Anlass war politische Kritik. Sie stellen klar: Bioenergie wurde berücksichtigt – die Analyse zeigt Optionen für eine effiziente Flächennutzung im Energiesystem.
Neue Publikationen
Performance Analysis of an Onboard PV System on a Demonstrator Light Commercial Vehicle in Hannover, Germany
Patel, Neel and Sovetkin, Evgenii and Pieters, Bart and Bittkau, Karsten and Ding, Kaining and Peibst, Robby and Fischer, Hilke and Reinders, AngèleDegradation of PGM and PGM-free Coatings on PEMWE Porous Transport Layers
Stein, Lukas and Dittrich, Arne and Walter, Dominic C. and Trinke, Patrick and Bensmann, Boris and Hanke-Rauschenbach, RichardForschung zu gebäudeintegrierter Solartechnik am ISFH
Schulte-Huxel, H.PV-Design-Fassadenelement: Entwicklung eines PV Moduls auf Aluminium zur Gebäudeintegration
Meyer, K.Strategisches Positionspapier zur Stärkung der Solarindustrie: Impulse für die Koalitionsverhandlungen 2025
Forschung am ISFH
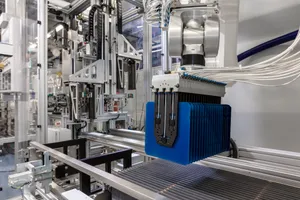
Siliziumsolarzellen und -module
Vom Silizium-Wafer bis zum PV-Modul: Unsere Forschung vereint Materialverständnis, Zell- und Modultechnologie, Qualitätssicherung und Fertigungstechnik für eine hocheffiziente, kostengünstige und ressourcenschonende Photovoltaik-Produktion.
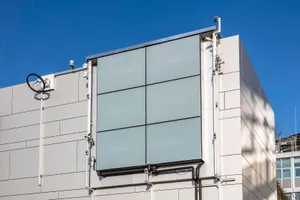
Gebäudeintegration
Gebäudeintegrierte Solarthermie, Photovoltaik und Photovoltaik-Thermie – funktional, ästhetisch und effizient. Wir entwickeln Lösungen für Fassaden, Dächer und neue Energieanwendungen.
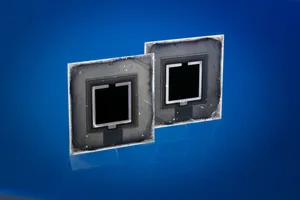
Tandemsolarzellen und -module
Wir entwickeln innovative Tandemsolarzellen-Konzepte mit Fokus auf höchste Effizienz, industrielle Umsetzbarkeit und die Reindustrialisierung der PV-Produktion in Europa.
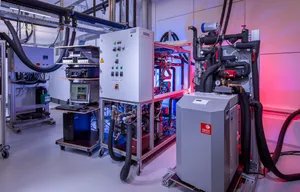
Gebäudeenergiesysteme
Innovative Energiesysteme für Gebäude: intelligent vernetzt, solar unterstützt und bereit für die klimaneutrale Zukunft.
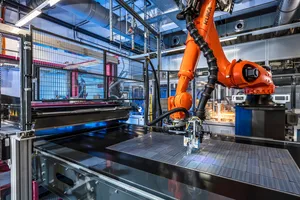
Fertigung und Spezialproduktion
Wir entwickeln am ISFH digitale, flexible und kosteneffiziente Technologien für die Produktion von Solarzellen und (maßgefertigten) PV-Modulen.
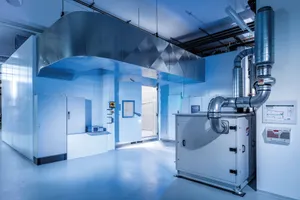
Wärmepumpen
Wir erforschen Wärmepumpen zur Versorgung von Gebäuden und Quartieren und thermischen Energiesystemen – mit Simulation, Komponentenanalyse und realen Praxistests.
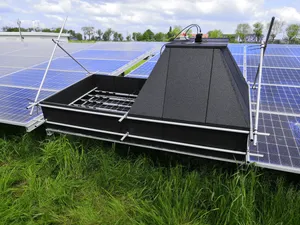
Zuverlässigkeit von Photovoltaik
Wir prüfen, wie zuverlässig neue Solarzellen, Materialien und PV-Module unter realen Bedingungen funktionieren, sei es im Labor, Freifeld oder mit Spezialmodulen.
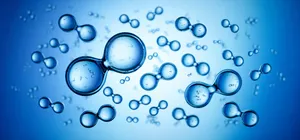
Wasserstoff
Wir bringen grüne Wasserstofftechnologie voran: durch neue Katalysatoren, innovative Materialien mittels Protonen-Austausch-Membran-(PEM)-Elektrolyse und Unterstützung der Industrie bei der Skalierung neuer Lösungen.
Unser Service im CalTeC
Als von der DAkkS anerkanntes Labor bietet das ISFH CalTeC präzise Kalibrierungen und Prüfungen für Solarzellen, solarthermische Systeme und Spektroradiometer – nach internationalen Normen wie ISO, IEC und EN. Neben akkreditierten Services unterstützen wir Sie auch mit individuellen Prüfungen und Entwicklungsbegleitung.
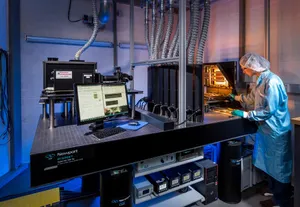
Haben Sie eine Frage zum ISFH?
Wir helfen Ihnen gerne weiter! Sie können die konkreten Ansprechpartner zu unserer Forschung kontaktieren oder uns über unseren allgemeinen Kontakt erreichen.